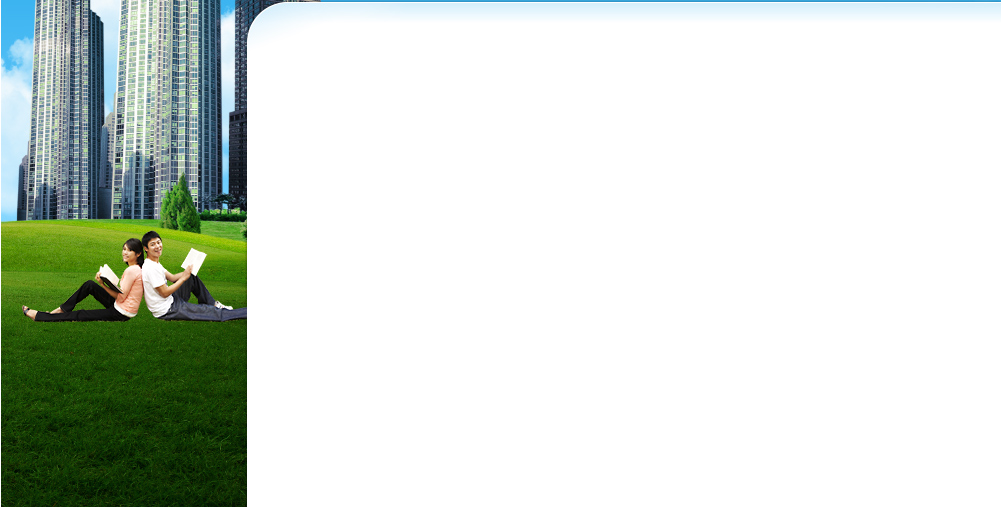
公司地址:海南省三沙市富联娱乐电机股份有限公司
电话:15936212002
传真:400-822-6211
邮箱:595588519@qq.com
集团网址:http://www.hlzsy.cn
首页、(天火注册)、首页仪器信息网摆线针轮行星减速器专题为您提供2023年最新摆线针轮行星减速器价格报价、厂家品牌的相关信息, 包括摆线针轮行星减速器参数、型号等,不管是国产,还是进口品牌的摆线针轮行星减速器您都可以在这里找到。 除此之外,仪器信息网还免费为您整合摆线针轮行星减速器相关的耗材配件、试剂标物,还有摆线针轮行星减速器相关的最新资讯、资料,以及摆线针轮行星减速器相关的解决方案。
国内外机器人关节测试技术现状及展望石照耀,程慧明引言2021年中国机器人行业市场规模为1306.8亿元,预计2022年行业市场规模将达1712.4亿元,同比增长31.0%,增速全球领先。关节是机器人执行姿态控制的执行部件,其性能对机器人的整机性能和可靠性起决定性作用。按动力来源可以分为液压、气动和电机驱动三大类,本文主要介绍电驱动关节。关节主要由传动、控制和传感部分组成,其中传动部分由电机、减速器和结构件组成,控制部分由驱动模块及通信模块组成,传感器部分使用了位置、力矩、电流和温度等。随着机器人应用领域与规模的快速扩张,关节种类不断增加、性能也不断优化。与此相适应,对关节性能的表征、测试和评价也成为了当前的研究热点。全面考察机器人关节测试技术现状,发现整体上呈现出四个特点:(1)测试技术多来源于减速器和电机测试技术,缺乏完全适用于关节的整机测试技术。(2)国内外研发的测试设备主要针对大中型关节,而针对小型或微小型关节的测试技术和设备较少。(3)对关节的测试多集中在减速器和电机上,而不是将关节作为一个整体进行测试。(4)测试参数不全面,多集中于关节的定位精度、速度响应能力上,缺少对其传动精度参数、电参数及其与机械参数的测试和融合分析。机器人关节的结构不简单,同时蕴含着复杂的能量转化、能量传递以及运动控制等问题。应用场景的多样化对机器人主机装备的运动性能精度、负载控制、能耗效率、振动噪声、服役寿命等性能提出了更高的目标,这对关节的综合性能提出了进一步的要求。因此对机器人关节进行综合性能测试,获取关键性能指标,并为设计提供指导具有重要意义。1关节分类1.1类型机器人关节的种类众多,可大致划分为刚性关节和弹性关节两类。刚性关节主要由电机、高传动比减速器、编码器、力矩传感器和控制器等组成。Albu-Schaffer等为德国宇航局的轻量机器人设计的机器人关节,包括无刷电机、谐波减速器、绝对编码器、增量编码器、刹车和力矩传感器等,如图1所示。SamuelRader等设计的机器人关节装有陀螺仪,可以实现更加精准的姿态控制。由于材料和设计上的限制,刚性关节存在功率密度值不高和机器人受冲击情况下关节强度不够的问题,因此刚性关节在使用上存在一定的局限性。图1刚性关节弹性关节分为串联弹性关节与并联弹性关节两种。弹性关节的设计原理来自于Hill肌肉三元素力学模型,以求更好的模拟人体肌肉功能。Pratt首先提出了串联弹性关节的概念,串联弹性关节在减速器和电机之间增加弹性连杆,用于降低外部冲击载荷和储存能量。Vanderborght等设计了可平衡位置的关节,Negrello等设计了新型关节,并进行了负载能力和抗冲击能力实验,如图2所示。并联弹性关节是在机器人整机上增加并联弹性连杆,通过和关节共同配合,来达到释放冲击和储能的功能。图2弹性关节1.2技术要求机器人应用场景的多样化对关节的技术提出了不同的需求,以刚性关节为例,大致可以分为两类,如表1所示。表1关节技术要求第一种类型关节被广泛应用于教育机器人、玩具机器人和餐饮机器人等,对关节的传动精度要求相对较低,通常对整机的回差要求小于60′。减速器的齿轮模数在0.2mm-0.5mm之间,材料以金属和塑料为主,种类有平行轴齿轮减速器、行星齿轮减速器、面齿轮减速器,其中平行轴齿轮减速器较为常见,部分减速器内部会增加离合机构,当机器人跌倒减速器受到冲击时,用于保护内部结构,该类型关节通常没有力矩传感器。第二种类型的关节广泛应用于大型双足服务机器人、工业机器人和航空航天领域的空间机械臂等,此类关节对传动精度要求较高,通常对整机的回差精度要求是小于3′。其减速器的传动形式主要有行星减速器、摆线针轮减速器、谐波减速器,其中谐波减速器最为普遍。电机多使用直流无刷电机和永磁同步电机,在安装上多采用无框形式。位置检测传感器有光栅编码器、磁编码器,力矩传感器有应变扭力计。2关节测试方法现状机器人关节的性能主要反映在传动精度、机械参数、响应参数和电参数等指标上。减速器和电机作为关节的重要部件,两者测试技术的发展为关节测试技术提供了借鉴,但减速器和电机的质量不能反映关节整机的质量,因此对关节的测试应面向整机。2.1传动精度传动误差和回差是评价关节运动输出精度的主要指标。传动误差既反映了传动部分制造误差和安装误差,又反映了其抵抗外界环境(如温度、负载等)的能力。回差则反映了关节传动系统中的间隙,其主要由空程回差、弹性回差、温度回差等组成。2.1.1传动误差(1)测试方法对精密减速器等传动链的传动误差测试技术研究可以追溯至上世纪50年代,K.Stepanek研制出基于磁栅式传感器测试齿轮机床动态误差的设备。C.Timmc基于光栅式传感器,通过将旋转角位移转换成相应电信号输出以得到传动误差的一种测量方法。黄潼年先生提出了“单面啮合间齿测量法”,发明了齿轮整体误差测量技术。彭东林提出一种时栅传感器,用于对传动误差进行测量。国标GB/T35089-2018对机器人用谐波齿轮减速器、行星摆线减速器、摆线针轮减速器等精密传动装置的试验设备、传动误差试验方法及其数据处理方法做出规定。机器人关节的传动误差测试技术来源于上述方法,关节的传动误差是指:对应伺服电机任意转角,关节的实际输出转角与理论转角之间的差值,传动误差曲线机器人关节传动误差示意图文献[3]基于光栅法对关节的传动误差进行测试。文献[4]利用高精度光栅测量关节的输出角度,关节电机编码器测量输入端角度,实现了对关节整机传动误差的测试。(2)测试难点关节是一种复杂的机电一体化产品,由于在工作原理、机械结构、传感器配置和控制方式等方面不同于其他的齿轮传动机构,使得对关节传动误差的测试也存在不同,因此在测试方法上带来了一系列的不确定和难点问题。根据GB/T35089-2018对精密减速器传动误差测试设备的规定,在减速器的输入端和输出端分别利用高精度角度编码器采集角度数据。对关节传动误差的测试,是以关节整机为测试对象,关节输入端角度数据的采集依赖于关节电机编码器。部分关节编码器精度较低或者没有安装电机编码器,因此在此类关节传动误差的测试中如何保证输入角度的有效性是一个难点问题。目前的解决方案有两种,一是文献[4]中所利用的等时间间隔采样方式,该方法可以在一定程度解决编码器精度不足的影响,但该方法可能存在时间滞后和关节本身不支持该模式的问题;二是以控制器发出的指令角度为输入端角度,即以理论转角为输入端角度,该方法符合关节传动误差的定义。综上所述,关节的传动误差测试方法多来源于精密减速器等传动装置,但由于关节本身的特点,使得其传动误差的测试方法具有一定的特殊性。2.1.1回差(1)测试方法机器人关节的回差是指:关节的输入端伺服电机运动方向改变后到输出端运动方向跟随改变时,输出端在转角上的滞后量。按照测试原理的不同,对关节回差的测试可以分为静态测试和动态测试两种。静态测试:是指将关节的输入端固定,通过输出端加载、卸载,获取滞回曲线而完成的回差测试,滞回曲线所示。输入端固定,给输出端逐渐加载至额定转矩后卸载,再反向逐渐加载至额定转矩后卸载,记录多组输出端转矩、转角值,绘制完成的封闭的转矩-转角曲线滞回曲线示意图在关节输出端不同位置进行回差测试,获得各个位置的回差,由此获得静态测试的回差曲线静态测试的回差曲线动态测试法:通过测试关节的双向传动误差曲线,获取回差曲线而完成的回差测试。首先测出关节正向传动误差曲线,使输入端正向多转一定的角度后反向旋转,然后在相同条件下测出关节反向传动误差曲线中反向传动误差曲线与正向传动误差曲线对应点的代数差即构成回差曲线]采用动态测试方法对小型关节进行了回差的动态测试实验,并和静态测试进了对比,发现结果大体一致,可以在一定程度上进行相互印证。图6双向传动误差曲线)测试难点同传动误差测试类似,关节回差的测试也不同于精密减速器等传动装置,对测试方法的研究也需要从关节本身的特点来考虑。(1)关节带电状态是影响关节回差测试的一个重要因素,按照关节回差静态测试方法的定义,需要将关节的输入端固定,即电机轴抱死。关节上电后电机轴抱死,在静态测试过程由于电机反向电动势的阻碍,会对测试结果产生影响。(2)角度编码器精度和有无问题同样影响关节的回差动态测试,按照定义需要获得双向传动误差曲线,进而获得回差曲线。在实际测试过程中,若采用等时间间隔采样的方式,则会存在采集点无法对齐的问题。若采用理论角度为输入端角度的方法,则存在测试不连续的问题。(3)联轴器变形会影响关节回差测试结果,在加载测试中需要对联轴器变形进行补偿。2.2机械参数2.2.1启动转矩与反启动转矩测试机器人关节的启动转矩测试是指关节的输出端在无负载情况下,关节内部的电机缓慢进行转动,至关节的输出端转动,期间利用关节内部的力矩传感器采集转矩变换情况,利用测试设备的高精度角度传感器来实时判断关节输出端的转动情况,取转矩的最大值为启动转矩,测试曲线所示。需要注意的是若关节内部没有力矩传感器则无法进行启动转矩和反启动转矩测试。机器人关节的反启动转矩测试是指关节的输入端在无负载情况下,测试设备的加载电机缓慢进行转动,直至关节的输入端转动,期间利用测试设备的力矩传感器采集转矩变化情况,利用关节内部的输入端角度传感器实时判断关节输入端的转动情况,取转矩的最大值为反启动转矩,测试曲线所示。需要注意的是对关节的反启动转矩测试要在不带电下进行测试,因为电机在带电状态下反向转动会存在反向电动势,对关节转动存在阻碍。图8启动(反启动)转矩曲线工作区工作区用转速和转矩组成的二维平面坐标区域表示,如图9所示。关节运行时温度不超过关节允许最高温度,能长期工作的区域为连续工作区。图中连续工作区域是由关节的发热、机械强度、以及关节内驱动器的极限工作条件限制的范围。超出连续工作区,允许关节短时过载运行的区域为断续工作区。图9工作区2.3响应参数2.3.1位置响应频带宽度根据JB-T10184-2000的规定,对关节位置响应频带宽度的测试应按照如下方式。在给定某一恒定负载的情况下,关节输入正弦波信号,随着正弦波信号频率逐渐升高,对应关节位置输出量的幅值逐渐减小同时相位滞后逐渐增大,当相位滞后增大至90°时或幅值减小至输入幅值的1/根号2时的频率即为系统位置响应频带宽度。2.3.2正/负阶跃输入的位置响应时间关节在空载条件下或按照试验要求加载某一恒定负载(根据需求确定转动惯量和扭矩大小)。外部控制器发送由0到1的正阶跃信号给关节,并同步读取角度传感器的数据,记录关节从阶跃信号发出至位置达到0.9的时间;重复上述试验,取多次试验的平均值即为关节的正阶跃输入的位置响应时间,测试曲线正阶跃输入的位置响应时间同理,外部控制器发送由1到0的负阶跃信号给关节,并同步读取角度传感器的数据,记录关节从阶跃信号发出至位置达到0.1的时间;重复上述试验,取多次试验的平均值即为关节的负阶跃输入的位置响应时间,测试曲线负阶跃输入的位置响应时间2.4电参数电参数测试用于反映关节在工作状态下电流、转速、功率、效率与转矩之间的关系。电参数测试分为恒定加载测试与梯度加载测试。恒定加载测试是指关节输出端施加某一恒定负载的情况下,测试关节的电流、转速及转矩变化情况;梯度加载测试是指关节输出端梯度加载的情况下,测试关节转矩与电流、转速、效率、输出功率之间的关系,获得相应的特性曲线恒定加载测试恒定加载测试的目的是为检测关节在空载或稳定负载情况下,其瞬时电流、瞬时转速及瞬时转矩的波动情况,上述参数测试原理及测试曲线梯度加载测试梯度加载测试的目的是为检测关节在最高转速下,关节输出端负载从0Nm开始等时间梯度加载至堵转力矩为止的过程中,关节的电流、转速、效率、输出功率之间的关系,获得转矩—电流曲线、转矩—转速曲线、转矩—输出功率曲线、转矩—效率曲线以及关节最佳工作区域综合曲线,上述参数测试原理及测试曲线大中型关节测试设备在工业领域内成熟的商用大中型关节测试设备不多,本文列举多型大中型关节测试设备,从测试范围、测试功能、测试精度、测试原理以及测试数据运用五个方面进行对比,如表4所示。表4大中型关节测试设备由上表可知,大中型关节测试设备基本以单一类型性能参数测试为主,涉及定位精度、响应参数和机械参数,测试技术主要借鉴电机测试技术,少量来源于精密减速器测试技术,存在测试项单一,功能不完善等不足。在测试数据运用方面,主要目的为验证关节机械设计和运动控制算法的可靠性和有效性。目前面向大中型关节的测试设备正朝着综合性能测试和云端测试的方向发展,作者团队所研制的新型机器人关节综合性能测试机可以实现对关节传动精度、机械参数、响应参数、电参数和抗干扰等性能参数的综合测试,测试机的性能指标如表5所示,测试机如图12所示。表5新型机器人关节综合性能测试机图12服务机器人小型关节综合性能测试机利用该测试机实现了对关节性能全面测试,相关测试结果如图13所示,分别为传动误差、抗干扰性能和阶跃响应测试。图13关节测试测试机还具备云测试与数据云交互的功能,相关架构如图14所示,将关节测试中涉及的测试设备、传感器、控制软件、分析方法、测试方法、测试数据和辅助设备虚拟化为服务资源,通过通用的硬件设备接口和软件接口,依托云平台,实现了各测量资源统一的、集中的信息化和智能化组织管理和运用,最终面向用户提供个性化的测试服务和体验。图14关节云测试架构3.2小型关节测试设备小型关节测试的难点主要表现在:(1)传感器精度问题,小型关节内部的传感器精度较低,影响测试结果的准确性;(2)传感器缺乏问题,部分小型关节因体积限制,使得关节内部无法安装传感器,导致无法进行测试;(3)外形尺寸小:因小型关节的外形尺寸小,导致配套的测试设备存在夹具设计困难,外部传感器无满足尺寸要求等问题。作者团队在一定程度上解决了上述问题,研制了面向服务机器人小型关节的综合性能测试机,填补了国内的空白,其测试关节参数如表6所示,测试机的情况如表7所示。表6小型关节参数表7小型关节测试设备参数测试机如图15所示,主要由被测关节、高精度光栅、力矩传感器、电力分析仪和负载电机等组成。利用测试机对小型关节的回差、电参数和反启动转矩进行测试,相关测试结果如图16所示。该测试机主要解决了三个问题,一解决了小型关节测试手段缺乏的问题;二解决了小型关节整体性能测试难的问题;三解决了关节测试项目单一的问题。图15服务机器人小型关节综合性能测试机图16能测试机小型关节测试综上所述,在机器人关节测试设备研发领域存在测试项单一,测试数据运用不足等的问题,考虑到关节对于机器人市场的重要性和特殊性,对其测试技术的研究和测试设备的开发越发的迫切。4关节测试技术难点和发展趋势机器人关节经过了三十多年的发展,机器人主机应用场景的多样化对其关节的性能指标提出更多的需求,相应的为了适应不同场景,关节的结构配置也发生了众多变化。这对关节测试技术提出了更高的要求,关节测试技术面临的难点问题急需克服,下一步的发展方向需要深入讨论。4.1关节测试技术难点机器人关节测试技术难点归结为以下六点:(1)面向关节的测试方法。前述测试方法多源于精密减速器和电机的测试,但关节的结构配置不同于二者,现有测试方法并未围绕关节的结构特点进行完善。同时考虑到关节结构本身的差异性,需要对刚性和弹性关节等不同类型关节的测试方法进行细化和适应性改变。随着关节应用场景的复杂化,还需要对关节进行抗冲击、抗过载和寿命等极限性能测试,但此类性能指标的测试方法尚处于空白阶段。(2)综合性能测试设备。关节是复杂的机电一体化产品,本身对机械设计,能量传递以及运动控制等提出了较高的要求,这要求测试设备能够实现综合性能测试,但目前多数测试设备只能对关节某一项性能参数进行测试。综合性能测试设备需要在机械设计、传感器配置和测试软件开发上满足传动精度、机械参数、响应参数和电参数测试的需求。(3)关节配置。在测试过程中,关节本身为输入端,其内部传感器的精度和有无在一定程度上决定测试结果的有效性。如前述所示,关节内部角度编码器的精度越高,关节传动精度测试的结果可靠性越高。(4)数据运用。表4和表6总结了部分关节测试数据运用情况,发现测试数据主要用于机械设计、控制算法的验证,并未深入的进行机理性研究,没有依托数据进行精度评价体系建设、误差溯源和性能预报模型的研究,测试在机器人关节设计、制造、使用中的核心作用未得到体现。(5)云平台还未利用。应该将云计算、机器学习、人工智能及多传感器数据融合等先进技术引入到关节测试系统和健康监测中,提高关节测试的效率,能够提高关节行业产能和产品质量,增强集成系统和终端用户的故障决策能力。(6)测试方法标准化。目前市面上没有一部成熟的关节测试技术标准,相关测试原理,测试方法和测试设备来源于生产和研发机构的摸索。机器人关节行业的飞速发展对关节测试技术标准提出了需求,关节本身的技术要求又对标准的制定提出了更高的要求。4.2关节测试技术的发展趋势机器人关节测试技术的发展趋势可以归结为四点:(1)需要打通机器人整机测试技术与关节测试技术的壁垒。机器人主机厂商重视机器人整机测试技术,忽视关节测试技术的重要性。机器人关节主机厂商,重视关节本身的测试技术,忽视如何从机器人整机角度去考虑测试技术,因此打通两者测试技术的壁垒显得尤为迫切。而打通两者壁垒的关键是找到之间的关系,既一方面通过对机器人整机进行测试,可以反映某一关节的性能情况。另一方面通过对某一关节进行测试,可以反映出机器人整机的性能。故如何将机器人整机测试和关节整机测试进行融合是今后一个新研究方向。(2)重点研究传动精度测试技术。在相当长的一段时间中,工业领域对关节的测试目的是探究关节的负载大小、抵抗干扰能力等,对传动精度的要求较低。随着市场对高精度机器人需求的增长,相适应的对关节传动精度要求也越来越高,因此面向关节传动精度的测试技术是研究的重点。(3)对极限性能测试技术提出了需求。随着机器人工作环境越发复杂,对机器人关节的极限性能提出了更多需求。但与之相矛盾的是目前对关节的抗冲击、抗过载和寿命等性能指标的测试技术几乎为空白。因此解决这个矛盾,满足极限性能测试的需求是今后一个时期的核心问题。(4)需要建立面向机器人关节的测试标准。目前工业领域对机器人关节的测试标准呼声较高,需要行业内加强合作,深入研究关节测试方法,共同推进面向全局的机器人关节测试方法标准的建立。5结论本文围绕机器人关节测试原理、测试方法和测试设备三方面对关节测试技术进行了归纳总结。关节测试技术多源于精密减速器和电机测试技术,但单一部件的性能不能反映关节的质量,需要对关节整机进行测试。在关节传动精度测试中,关节内部角度编码器的精度和有无以及关节电力响应速度等问题都会影响测试结果,这也是关节传动精度的测试难点。总结了测试设备现状,发现了行业对关节测试设备需求的紧迫性。对测试技术的难点问题进行了分析,指出了测试方法不完善、缺乏综合性能测试设备、关节配置不足、数据运用不足、云平台技术缺乏以及还未标准化六个难点问题。展望了关节测试技术的发展趋势,发现正朝着解决测试技术的难点的方向发展。(省略参考文献49篇)
一、前言根据自有设备情况选用公司齿轮测量机、三坐标测量机作为数字化设备,分别对双联行星轮对齿精度进行测量。通过分析测量过程及测量结果,对三坐标测量机间接测量法进行改进,即通过对大小齿轮轮廓进行扫描,构造虚拟量棒直径计算对齿角度偏差,并根据这种测量方法编制了三坐标自动测量程序,提高了检测效率及准确性,保证产品的合格率至98%以上。二、实施背景(一)背景近年来,为降低矿山运输行业成本,提高效率,大型工程运输车开始设计生产,其中轮式自卸车比较热门,一直占据市场主导地位。当前,全球每年轮式自卸车销售额高达100亿美元以上,并且连续6年保持30%的增长率,足以说明一个新兴品类正在崛起。(二)现状轮式自卸车电动轮组成的主要部件为双联行星轮。行星齿轮传动与普通齿轮传动相比,具有重量轻、体积小、传递功率大、结构紧凑、承载能力高等一系列优点,在工业领域应用广泛。在行星传动的各种型式中,NW、NN及WW三种型式的行星齿轮为双联齿轮,当前国内研制和承接的轮边减速器产品中,NW型双联行星轮组的制造工艺难度系数最大。目前,只有GE、西门子等极少数国际大公司具备制造高品质双联行星轮组的能力,形成市场垄断,利润高达500%。最近几年,国内研制了多种双联行星轮组对,但制造过程复杂,工艺和产线瓶颈较多。大多数公司只能选择自行配对组装,但却无法满足与客户整机零件的互换,与行业中成熟产品存在较大差距,产品的销价差别也很大。(三)实施的紧迫性目前,中车戚墅堰所已涉及共计6款双联行星轮的研制,双联行星轮不仅可以作为零部件安装在总成上,还可以作为成品进行销售。通常双联行星轮需要经过热套、精磨轴承档、磨齿修正三个工序,每个工序都要检测对齿精度,只有保证每次检测的稳定和效率,才能使成品的对齿精度控制在顺逆30秒以内。为攻克目前产品中对齿精度检测的难点,本文对轮边减速器中的行星轮组对齿精度的相关工艺及检测要求进行了讨论分析,助力企业有效地提高生产效率,降低质量风险,固化生产周期并降低生产成本。三、测量方法及改进(一)间接测量方案及参数确定1.双联齿轮对齿技术简介行星齿轮机构传动是指二个或三个双联行星齿轮工作时与太阳轮、内齿轮同时啮合而形成的传动系统。双联行星齿轮对齿在技术条件上一般要求上下联的齿或槽中心对正,常用的对齿和测量方法是用插齿刀对齿,用圆柱棒进行偏差测量。2.测量设备配置检测设备配置如下表1所示,三坐标测量机是20世纪60年代发展起来的一种高效率的新型精密测量仪器。它的优点是:(1)通用性强,可实现空间坐标点的测量,方便地测量出各种零件的三维轮廓尺寸和位置精度;(2)测量精度可靠;(3)可方便地进行数据处理和过程控制。因此,它被纳入自动化生产线和柔性加工线中,并成为一个重要的组成部分。齿轮测量机主要用于测量齿轮的轮齿精度,包括齿形、齿向误差、周节累积误差、径向跳动误差等,测量精度高。表1检测所用设备设备名称型号生产厂家三坐标测量机MMZG303020德国蔡司ZEISS齿轮测量机P65德国克林贝格3.测量参数的确定选用1Z057双联行星轮作为测量件,它是由小行星轮和大行星轮组合而成的。(如图1)图11Z057双联行星轮选用三坐标测量机进行对齿精度测量时,首先要确定测量圆柱棒的直径。通过查阅1Z057双联行星轮的设计蓝图,了解大小行星轮的参数,再根据参数信息计算最佳圆柱棒直径进行测量。为保证测量结果的准确性,量棒直径不可太大,也不可太小;若直径太大,与齿廓的接触点有可能超出大径,若直径太小,则量棒外圆将与槽底接触。以上两种情况都无法得出正确的测量结果。为避免这些情况,选择量棒直径时,应使量棒外圆与齿廓的接触点落在分度圆及其附近的任意位置上,一般在距小径的(1/3~2/3齿高之间为宜。当量棒外圆与齿廓的接触点落在分度圆上时,可通过公式1得出量棒直径。公式(1)其中dp是量棒直径,db是分度圆直径,α是齿形角,Z为齿数,对于渐开线标准圆柱齿轮db=mz;小行星轮模数为8.367,齿数为17,齿形角为25度。经计算最佳量棒直径为φ16.771;大行星轮模数为8.175,齿数为72,齿形角为25度。经计算最佳量棒直径为φ15.797。4.间接测量方案根据公式(1)计算结果,我们选用φ16的量棒进行间接测量,测量方法如图2。图2测量小行星轮(左);测量大行星轮(右)先扫描上下两个轴承档连成公共轴线的量棒卡入齿槽内,用探头确定量棒中心位置,建立坐标系,计算出上下中心的偏移量,得出对齿角度偏差。图3为测量数据报告,根据偏移量的正负值确定顺逆方向。图3测量数据5.数据验证选用齿轮测量机进行测量,首先找正双联齿轮的轴承档,输入大小行星轮参数,选择角度测量软件,自动扫描轴承档,确定基准中心线,然后扫描大小行星轮齿槽左右齿面的齿形轮廓和齿向轮廓,确定齿槽中心线,通过软件计算,得到偏转距离,从而得出对齿角度。测量过程如图4,数据报告如图5。图4测量小行星轮(左);测量大行星轮(右)图5测量数据6.数据对比及测量存在的不足通过量棒间接测量的对齿角度为44秒,而齿轮测量机测量结果为1分05秒。以齿轮测量机测量结果为参考值,两次测量存在21秒偏差,偏差交大。对比两种测量方法,间接测量法以手动操作为主,人为不确定性较大;齿轮测量机通过扫描齿形轮廓和齿向轮廓确定齿槽中心线,得出对齿角度,数据精准性较高,但是起吊、找正及测量时间较长,效率低下,无法满足生产进度。(二)对齿精度检测工艺优化改善间接测量法测量结果偏差较大,特对其进行改进。首先选取小齿轮的上端面作为空转方向,小齿轮上端圆作为圆心,小齿轮两边对齿的中心点作为旋转方向建立初定位坐标系;通过初定位坐标系,三坐标测量机能够快速准确地扫描工件的上下两个轴承档并使其公共轴线成为基准;再通过三坐标测量机运用未知曲线扫描功能对上下齿轮中部(即齿向最高点)的齿槽两边进行扫描,得到2条V形曲线)。构造与V形曲线相切的两个虚拟圆形,小行星轮选择直径为φ16.771的圆,大行星轮选择直径为φ15.797的圆(如图7)。以轴线作为基准,小行星轮虚拟圆圆心到轴线的连线作为方向基准建立坐标轴。通过计算两个虚拟圆圆心到轴线连线的夹角得出对齿角度。图6扫描程序图7小行星轮拟合圆(左);大行星轮拟合圆(右)表2双联行星轮对齿角度数据序号改进前(三坐标)改进后(三坐标)(齿轮仪)方向10’40”0’22”0’20”顺时针20’38”0’18”0’20”顺时针30’42”0’23”0’20”逆时针40’20”0’13”0’10”逆时针50’15”0’36”0’35”逆时针60’40”0’51”0’50”逆时针70’28”0’9”0’12”顺时针80’30”0’13”0’13”顺时针90’5”0’21”0’20”顺时针100’13”0’35”0’35”顺时针110’30”0’15”0’12”顺时针120’28”0’10”0’12”逆时针130’5”0’24”0’20”顺时针140’45”0’24”0’25”顺时针150’5”0’25”0’23”顺时针160’10”0’30”0’29”顺时针170’5”0’20”0’20”顺时针180’30”0’10”0’5”逆时针190’24”0’23”0’25”逆时针200’19”0’40”0’38”顺时针210’28”0’14”0’10”顺时针220’13”0’32”0’30”顺时针230’10”0’30”0’32”顺时针240’40”0’25”0’25”顺时针250’15”0’33”0’30”顺时针260’29”0’22”0’20”逆时针270’42”0’22”0’25”顺时针280’8”0’29”0’28”逆时针290’28”0’16”0’12”逆时针300’40”0’20”0’21”顺时针平均偏差0’16”0’2”表2为30件工件的测量数据,以齿轮仪测量结果作为参考值。对比可见,改进前的数据平均偏差为16”,改进后的数据平均偏差为2”,表明改进后三坐标测量数据的稳定性及精确度都有了进一步提升,与齿轮仪的测量数据偏差较小,满足设计要求,提升测试效率,为双联行星轮的加工提供了强有力的数据支持,也为公司打破垄断走向市场提供了关键的检测技术支持。四、实施效果及意义通过对间接法进行改进优化,三坐标测量机适用于各类型双联行星轮组的对齿精度检测。对齿精度检测工艺的优化,也大大提升了产品合格率,取得了巨大成效,主要有以下4个方面。1.双联行星轮对齿精度合格率达98%;2.双联行星轮制造成本降低10%,产品质量和市场竞争力获得极大提高;3.双联行星轮的检测周期缩短20%,由以前的2天以上缩短至1天;4.双联行星轮可实现90%成品的对齿精度在正负30秒以内,媲美GE、西门子等公司同类产品要求。参考文献[1]王兰群张国建.渐开线花键M值得测量及量棒直径的选择2005.9.1[2]张志宏张和平双联行星齿轮模拟装配2005.8.26[3]郭海风张丽双联行星齿轮对齿技术1994.1.1本文作者:中车戚墅堰机车车辆工艺研究所有限公司计量检测工程师蒋瑞骐
9月份将要实施的68个与仪器及检测相关标准——食品、冶金、医药领衔为了方便仪器及检测使用者查看9月份实施的标准,我们继续整理了即将实施的标准。本次整理除了即将实施的国家标准,还有行业标准和地方标准。一共有68个标准与我们仪器及检测相关,其中食品、冶金、医药三个领域领衔。食品将迎来史上“最严”农药残留检测标准GB2763-2021,食品安全GB23200四个标准也将实施。具体如下,需要的可以收藏。化妆品标准GB/T40146-2021化妆品中塑料微珠的测定食品标准GB2763-2021食品安全国家标准食品中农药最大残留限量GB23200.118-2021食品安全国家标准植物源性食品中单氰胺残留量的测定液相色谱-质谱联用法GB23200.119-2021食品安全国家标准植物源性食品中沙蚕毒素类农药残留量的测定气相色谱法GB23200.120-2021食品安全国家标准植物源性食品中甜菜安残留量的测定液相色谱—质谱联用法GB23200.121-2021食品安全国家标准植物源性食品中331种农药及其代谢物残留量的测定液相色谱—质谱联用法DBS34/003-2021食品安全地方标准食品小作坊卫生规范DBS42/002-2021富有机硒食品硒含量要求《食品农残国标GB23200系列汇编》-120个标准合集冶金标准GB/T39123-2020X射线和γ射线探测器用碲锌镉单晶材料规范GB/T39125-2020铈镁合金GB/T39523-2020精密行星摆线减速器扭转振动性能测试方法GB/T39135-2020建筑光伏玻璃组件色差检测方法GB/T39137-2020难熔金属单晶晶向测定方法GB/T39138.1-2020金镍铬铁硅硼合金化学分析方法第1部分:金含量的测定硫酸亚铁电位滴定法GB/T39138.2-2020金镍铬铁硅硼合金化学分析方法第2部分:镍含量的测定丁二酮肟重量法GB/T39138.3-2020金镍铬铁硅硼合金化学分析方法第3部分:铬、铁、硅、硼含量的测定电感耦合等离子体原子发射光谱法GB/T39143-2020金砷合金化学分析方法砷含量的测定电感耦合等离子体原子发射光谱法GB/T39144-2020氮化镓材料中镁含量的测定二次离子质谱法GB/T39145-2020硅片表面金属元素含量的测定电感耦合等离子体质谱法GB/T39146-2020耐火材料抗熔融铝合金侵蚀试验方法GB/T39148-2020回收铋原料GB/T39149-2020回收碲原料GB/T39150-2020回收硒原料GB/T39152-2020铜及铜合金弯曲应力松弛试验方法GB/T39153-2020亚稳分解强化铜-镍-锡合金棒材GB/T5801-2020滚动轴承机制套圈滚针轴承外形尺寸、产品几何技术规范(GPS)和公差值GB/Z39124-2020铅精矿化学分析方法锑含量的测定硫酸铈滴定法DB23/T2962-2021天然鳞片石墨石墨化度测定方法DB23/T2963-2021天然鳞片石墨中微量钙含量测定钙-偶氮胂Ⅲ分光光度法水产标准DB35/T1984-2021水产品乙酰甲喹及其主要代谢物鉴别技术规程计量校准标准JJG(苏)247-2021随机冲击速度测量仪检定规程JJF(苏)242-2021精密型液体浴试验设备校准规范JJF(苏)243-2021分布光度计校准规范JJF(苏)245-2021药品强光稳定性试验箱校准规范JJF(津)60-2021机动车尾气排放检测用五参数测试仪校准规范JJF(津)59-2021汽车行驶记录仪检定装置校准规范JJF(津)58-2021氟化物测定仪校准规范JJF(桂)94-2021电热恒温水浴锅校准规范医疗行业标准YY/T0285.6-2020血管内导管一次性使用无菌导管第6部分:皮下植入式给药装置YY/T0342-2020外科植入物接骨板弯曲强度和刚度的测定YY/T0611-2020一次性使用静脉营养输液袋YY/T0616.7-2020一次性使用医用手套第7部分:抗原性蛋白质含量免疫学测定方法YY/T0651.2-2020外科植入物全髋关节假体的磨损第2部分:测量方法YY/T0664-2020医疗器械软件软件生存周期过程YY/T0707-2020移动式摄影X射线机专用技术条件YY/T0809.2-2020外科植入物部分和全髋关节假体第2部分:金属、陶瓷及塑料关节面YY/T0953-2020医用羧甲基壳聚糖YY/T1293.6-2020接触性创面敷料第6部分:贻贝黏蛋白敷料YY/T1477.6-2020接触性创面敷料性能评价用标准试验模型第6部分:评价促创面愈合性能的动物2型糖尿病难愈创面模型YY/T1629.4-2020电动骨组织手术设备刀具第4部分:铣刀YY/T1629.5-2020电动骨组织手术设备刀具第5部分:锯片YY/T1631.2-2020输血器与血液成分相容性测定第2部分:血液成分损伤评定YY/T1693-2020牙科学上颌窦膜提升器YY/T1708.2-2020医用诊断X射线影像设备连通性符合性基本要求第2部分:X射线计算机体层摄影设备YY/T1737-2020医疗器械生物负载控制水平的分析方法YY/T1738-2020医用电气设备能耗测量方法YY/T1744-2020组织工程医疗器械产品生物活性陶瓷多孔材料中细胞迁移的测量方法YY/T1746-2020可吸收性外科缝线体外水解后断裂强力试验方法YY/T1751-2020激光治疗设备半导体激光鼻腔内照射治疗仪YY/T1754.1-2020医疗器械临床前动物研究第1部分:通用要求YY/T1754.2-2020医疗器械临床前动物研究第2部分:诱导糖尿病大鼠皮肤缺损模型YY/T1758-2020心血管植入物肺动脉带瓣管道YY/T1759-2020医疗器械软性初包装设计与评价指南YY/T1762-2020单髁膝关节置换假体金属胫骨托部件动态疲劳性能试验方法YY/T1765-2020全膝关节假体约束度测试方法其他标准GB/T40245-2021废弃防腐木材回收规范GB/T40139-2021材料表面积的测量高光谱成像三维面积测量法DB52/T1597-2021计量检测元数据及交互规范目前仪器信息网资料库有近70万篇资料,内容涉及检测标准、物质检测方法/仪器应用、仪器操作/仪器维护维修手册、色谱/质谱/光谱等谱图。资料库每月有近20万人访问,上万人下载资料,诚邀您分享手头上的资源,与人分享于己留香!
近日,江苏省认证评审专家组对江苏省减速机产品质量监督检验中心进行了计量认证和实验室资质认定。专家组成员首先听取了中心相关负责人的情况汇报,对计量认证和实验室资质认定的相关材料进行了详细审核,随后根据《实验室资质认定评审准则》对减速机整机性能检测系统、齿轮检测中心、光谱仪、材料试验机等相关设备进行了实验,并考查了相关工作人员从业资质和实验能力。经过审查,专家组对中心共认定了50个检测项目和42个检测参数,覆盖减速机整机、齿轮和金属材料等相关产品。专家组最后确认该中心实验室管理体系运行有效、仪器设备配备齐全、人员资质和操作技能均符合相关要求,一致同意江苏省减速机产品质量监督检验中心初步通过“双认证”。江苏省减速机产品质量监督检验中心为泰兴市的重点建设项目,泰兴市质监局承担相应建设任务,中心建成后主要为全省减速机相关企业提供各类检测服务,将有效推动减速机产业往“高精尖”方向发展。下一步,中心将全力以赴争取一次性通过省级中心验收。
4月1日,江苏省减速机产品质量监督检验中心建设项目通过省质监局专家评审组验收,并正式对外运营。这为泰兴减速机产业升级转型提供了有力的技术支撑。省减速机产品质量监督检验中心项目一期工程投资1500万元,建设标准检验用房3000平方米。按照国际先进、国内一流的要求,选用的齿轮测量中心、直读式光谱仪、整机试验台测试系统均引进国际领先的德国原装产品。目前,已具备200千瓦减速机整机检测能力,范围覆盖负载、超载试验、输出扭矩、传动比误差、传动效率、噪声、温升等项目,可满足目前国家标准和行业标准涉及的40种减速机整机检验,并具备对减速机及其它传动机械15种主要配件加工精度和热处理质量的检验能力,以及对铸铁、铸钢、合金钢、铜材、铝材中12种元素的无损分析。“泰兴减速机发展已有30年历史,是名闻遐迩的‘减速机之乡’,全市注册登记从事减速机及配套产品加工的企业达300多家,其中整机生产企业70家左右,行业年销售收入40多亿元,并拥有泰星、泰隆两家中国名牌产品生产企业。但检测检验能力一直跟不上减速机产业的发展水平。”泰兴质监局局长王坚告诉记者,2009年7月底,在省质监局的关心支持下,泰兴开工建设省减速机产品质量监督检验中心,并于今年1月上旬通过省计量认证和实验室资质认定,具备对外检验资质。“下一步,将计划投资4000万元,启动省减速机产品质量监督检验中心二期工程,建设500千瓦整机测试平台,进一步提升检测检验水平,争创国家级检测中心。”王坚介绍,借助中心强有力的技术支撑,力争未来3至5年减速机产业规模在现有基础上翻两番,达160亿元至200亿元。
由宝钢集团和深圳万测试验设备有限公司(万测集团WANCE)强强合作研发的国内首台超大能量10万焦瓦(J)全自动摆锤式撕裂冲击(DWTT)试验机在宝钢集团正式投用。这意味着万测集团-民族自主品牌,不仅在全自动摆锤式撕裂冲击试验上中进入世界领先行列,传承和弘扬了民族试验机领域的荣耀,还进一步提升了宝钢集团在高等级厚板管线钢方面的检测和试验能力,为宝钢的高规格钢材生产提供了试验设备。10万焦瓦全自动摆锤式冲击试验机是通过控制摆锤的下落,冲击厚板管线钢试样,观察撕裂钢板并对内部质量进行全面的分析来得到试验数据,为生产使用做好准备。据万测集团WANCE负责人介绍:该设备主要用于中厚板的动态撕裂试验(简称DT试验)。动态撕裂试验是指按相关标准试验时,将处于简支梁状态下的动态撕裂试样一次冲断,测量其吸收能量(即动态撕裂能:用以表征各特定厚度的金属材料抵抗动态撕裂的能力)和纤维断面率的试验。该试验机集机、电、自动控制技术于一体,实现了送料、取摆、冲击、断裂试样收集的全自动化过程。另外万测集团WANCE设计该试验机设有多道保护措施,大大提高了操作人员及设备使用的安全性。该试验机除了传统的钢铁生产企业,该试验机还广泛用于科研院所,大专院校等科研机构以及质检所等检测机构,解决了冲击能量不足导致的各种生产,研发问题。万测集团WANCE研发的该试验机冲击能量可从5000焦瓦(J),7500焦瓦(J),40000焦瓦(J),50000焦瓦(J)到10万焦瓦(J),测试范围扩大,可实现厚度在45毫米内X100材质管线钢的DWTT试验,填补了业界DWTT试验能力5万焦瓦以上的空白。采用摆锤式设计,虽然增加了制造难度,但有利于提升测试精度,并满足用户需求。万测集团WANCE和宝钢集团的专业技术人员不断攻关,不断创新,不仅解决了技术上的问题,还在设计上采用了全自动式设计提高了检测人员操作的安全性和效率。新设备的投用,不只是试验机品牌标杆万测集团WANCE的实力证明,也将提升宝钢高端厚板管线钢的检测和生产制造能力,是给民族试验机和钢铁制造业的一次赠礼!咨询电话两款机型主要功能:主要适用于铁素体钢、管线钢的DWTT撕裂试验,可以测出试样的撕裂能量。主要特点:1.高强度底座及机架,充分保证设备的强度及精度,有效减小冲击时的震动。2.具有三套挂摆装置,实现不用更换摆锤就可获得三种不同的冲击能量。3.全自动化控制,送样、冲击、挂摆、回收等动作可连贯完成。4.传动系统采用伺服电机作为扬摆的动力源,恒扭矩输出,挂摆准确。直接由摆线针轮减速机带动离合器,结构简单,减速比高,抗过载能力强,效率高,体积小,基本免维护等优点。5.具有送样及定位装置,送样迅速,定位准确,提高试验效率及安全性,有效减轻试验人员劳动强度。6.具有气动刹车装置,避免离合器高速时动作,有效减小离合器冲击磨损,从而大大延长其寿命。满足标准:1.GB/T8363-2007《铁素体钢落锤撕裂试验方法》2.ASTME436-03《StandardTestMethodforDrop-WeightTearTestsofFerriticSteels》3.APIRP*5L3-96《ConductingDrop-WeightTearTestsonLinePipe》4.GB/T3808-2002《摆锤式冲击试验机的检验》5.JJG145-2007《摆锤式冲击试验机》应用行业:冶金钢铁;机械制造;科研实验所;其它行业。原装配置:摆锤一个、送样装置一套、钳口刀刃一套可拓展配置:低温装置技术参数:
近日,江苏省减速机产品质量监督检验中心(泰兴)的检验人员深入企业帮助解难题,受到企业好评。据介绍,某企业前不久研制一款新型减速机以用于油田开发。但检验人员在对该型号减速机进行整机性能试验时发现,其变速换挡杆几何尺寸设计不合理,引起减速机运行不平稳、噪声大等问题。在江苏省减速机产品质量监督检验中心(泰兴)的检验人员与企业技术人员的共同攻关下,一举解决了难题,为新品上市赢得了宝贵的时间。近一年来,江苏省减速机产品质量监督检验中心(泰兴)不断加大设备投入力度,目前已具备200千瓦减速机整机检测能力,已为50多家企业产品开发、质量把关、开拓市场保驾护航。
导读“风暴”新一代电子万能试验机是三思纵横独立研发于2016年闪耀问世。能最大化满足用户试样试验需求,是各类金属、非金属材料试样试验的首选。目前已广泛应用于各种塑胶、橡胶、金属、航空航天、船舰、建工、军工、商检、高等院校等相关行业的试验测试。随着全球科学技术的快速发展及工业生产要求不断提高,之前相对冷门的试验机行业也迎来了春天,不断炫耀着其市场潜力和蓬勃生机。有数据显示,中国试验机市场销售总额每年可高达40亿人民币。行业的发展也带动了试验机技术的革新,目前相关技术已在测量技术、控制技术、计算机应用技术、全数字化技术等多个领域取得突破性的进展,这也促使我国电子万能试验机、微机控制液压万能试验机、电液伺服动静万能试验机、高频疲劳试验机等试验机产品有了进一步提升和发展。而这些新技术新产品也反过来为我国试验机产业发展起到了推动作用,催生了众多试验机企业。本文介绍的是行业领跑企业三思纵横一款新型电子万能试验机——三思纵横风暴系列。三思纵横风暴系列新一代电子万能试验机于2016年闪耀问世,国内首家可记录各种力学性能式样试验数据的电子万能试验机,该试验机率先引进西方先进技术,采用进口最新科学高能配件,历经多年结合试验机新产品市场需求研制而成,与国际研发接轨,独家研创,外形精美,操作方便,低耗高能,性能稳定可靠,能最大化满足用户试样试验需求,是各类金属、非金属材料试样试验的首选。广泛应用于各种塑胶、橡胶、金属、航空航天、船舰、建工、军工、商检、高等院校等相关行业的试验测试。首创横梁位移显示屏及手控盒装置国内首家独创横梁位移显示屏,实时采集横梁的绝对位置,显示横梁移动方向操作简洁,便于观察与纪录;手持式控制操作系统手控盒,可定位控制横梁位移速度以及配套的电子夹具的夹持控制,控制盒手柄上还携带与位移显示屏同步的数据显示,使试样测试操作控制更加直观简单。率先发明设计测控系统机箱国内首次大胆创新的设计,将测控系统与减速系统外置合一为精巧的机箱盒;有效避免试样中电子万能机带来的震动干扰,极大的降低密封部件的损耗;试验稳定,延长各个部件的寿命,长效使用减少维修;500000码高分辨率数字控制器;高于1000Hz数据采样速率,试验数据更精确。国际一流伺服电机与减速器动力系统采用国际最先进的技术,最新进口伺服电机和伺服系统,以及德国行星减速机,配以滚珠丝杠副传动系统;实现试验机移动横梁的上下直线运动,比传统涡轮减速机声音更小,传动速率更高,传动平稳、噪音低(低于50db),测试性能更优异。精简外观,注重细节1.3×1.1×2.35的机身尺寸,外观精悍简洁;全封闭铝制防护罩,无缝焊接,精制抛光工艺,华丽中彰显霸气!相对外观,三思更注重细节处理,让试验机的横梁、围板等以新面貌面世;轮辐式新型设计,受横向载荷、非对称载荷、弯曲和扭转力矩的影响非常小;结合高要求的选材及精细的加工工艺,使得设备精度高(从满量程的0.4%开始,精度为0.5级)、刚性好(150%过载无变形(无机械损伤)高精度传感器,其稳定性好,抗侧向冲击能力强;在不违规操作的情况下,正常使用10年以上精度不变),产品质量更可靠。据悉,该设备由深圳三思纵横科技股份有限公司自主研发生产,“三思纵横”是中国试验仪器行业唯一的国家级高新技术企业,中国领先的材料试验设备和材料试验解决方案的服务商。公司集研发、生产、销售和服务四位一体,专业提供一流的材料试验设备与专业的材料试验解决方案。“三思纵横”公司总部位于深圳,生产基地分别设在深圳和上海。在中国的主要城市设有13个办事处和6个服务中心,为客户提供全面贴近和贴心的服务。近几年,合金材料、聚合物材料、陶瓷材料、超导材料等新材料的开发与使用,极大地拓展了试验机的应用领域。而试验机产业要想取得良性发展,未来就必须注重技术创新,掌握关键技术。未来试验机试验对象将会从材料、零部件扩展到整机、整车、系统、重大设施和各类工程项目。企业的中心实验室、质检部门、生产现场、工程项目的施工现场也将会逐渐应用试验机。线连续、实时、自动化实验方式成趋势,实验理论也会不断提升指导技术创新。未来模块化、系列化、共用化、特种、专业化、动化、智能化、网络化多方向发展试验机,将会成为试验机发展主流趋势。三思纵横将继续引领行业潮流,不断突破,不断创新,竭诚服务于客户!
为落实《国家中长期科学和技术发展规划纲要(2006—2020年)》《国家创新驱动发展战略纲要》和《中国制造2025》等规划,国家重点研发计划启动实施“制造基础技术与关键部件”重点专项。根据本重点专项实施方案的部署,编制2019年度项目指南。本重点专项总体目标是:以高速精密重载智能轴承、高端液压与密封件、高性能齿轮传动及系统、先进传感器、高端仪器仪表以及先进铸造、清洁热处理、表面工程、清洁切削等基础工艺为重点,着力开展基础前沿技术研究,突破一批行业共性关键技术,提升基础保障能力。加强基础数据库、工业性验证平台、核心技术标准研究,为提升关键部件和基础工艺的技术水平奠定坚实基础。通过本专项的实施,进一步夯实制造技术基础,掌握关键基础件、基础制造工艺、先进传感器和高端仪器仪表的核心技术,提高基础制造技术和关键部件行业的自主创新能力 大幅度提高交通、航空航天、数控机床、大型工程机械、农业机械、重型矿山设备、新能源装备等重点领域和重大成套装备自主配套能力,强有力地支撑制造业转型升级。本重点专项按照“围绕产业链,部署创新链”,从基础前沿技术、共性关键技术、应用示范三个层面,围绕关键基础件、基础制造工艺、先进传感器、高端仪器仪表和基础技术保障五个方向部署实施。专项实施周期为5年(2018—2022年)。1.基础前沿技术类1.1多维融合感知智能轴承基础原理与方法研究内容:研究智能轴承动态运行信息演化与传递机理 研究智能轴承集成感知机制与多维数据融合算法 研究智能轴承宽频高效自供电/无线供电原理与设计方法 研究智能轴承信息的高效、低功耗、高可靠传输原理与处理技术 研制多维融合感知智能轴承样机,并在数控机床、风电、轨道交通等行业开展试验验证。考核指标:开发面向数控机床、风电和轨道交通等领域的智能轴承原理样机3类,其中至少1类具备自供电/无线供电功能 典型故障检测类型≥3类,识别率≥90% 温度范围-50℃~300℃,精度优于1% 振动范围± 100g、± 300g、± 500g(各行业选1项),精度优于1% 载荷范围0~100kN、0~500kN、0~1000kN(各行业选1项),精度分别优于1%、2%、3%。1.2高性能轴承动态和渐变可靠性设计理论研究内容:研究滚动轴承渐变劣化(如疲劳和磨损等)规律和内外部振动行为 研究渐变失效和振动效应交互影响机理,建立动态和渐变可靠性设计模型及相关理论 研究滚动轴承可靠性设计技术及试验测试装置,并开展相关试验。考核指标:开发滚动轴承可靠性设计方法1套 构建滚动轴承的故障模式、失效案例、可靠性设计的数据库,覆盖疲劳、磨损、振动失效模式和可靠性设计数据10种以上 可靠性试验测试装置1套,完成3种典型产品的可靠性试验。1.3液压元件及系统智能化基础技术研究内容:研究电液深度融合的智能液压元件及动力单元,探索液压元件内部流量、压力、温度和位移等信息的集成测量新技术 研究多液阻独立控制的离散型液压元件的强非线性控制与适应调节机制 研究液压元件及动力单元的服役性能与寿命预测、典型应用案例的安全风险评估方法。考核指标:工业用有线或无线可编程电调制液压阀样机2种以上,具备介质的流量、压力、温度等测量功能,综合测量精度优于1% 液阻离散独立的智能液压阀控制器、液压阀样机及测量系统,系统控制精度优于3% 动力单元具有在线状态监测、故障诊断、服役性能与寿命预测等功能,故障诊断覆盖率不低于80%。1.4齿轮传动系统动力学基础理论及其健康监测研究内容:研究齿轮传动系统非线性动力学特性、几何与运动误差回溯、振动噪声预估与主动控制理论与方法 研究齿轮性能退化规律和典型损伤机理、监测信号解耦及故障诊断方法,建立多维监测参数特征与健康状态的映射关系 开发传动系统健康状态监测系统,并在风电等领域进行试验验证。考核指标:建立齿轮传动系统动力学优化方法,完成不少于1种产品动力学优化 开发传动动力学仿线套,仿线% 研制传动系统健康监测样机1套,故障监测准确度不低于90%。1.5新型高性能精密传动基础理论与技术研究内容:研究零隙精密传动及大速比传动新原理与新构型 研究相应的数字化设计方法、啮合副复杂曲面制造关键技术 开展传动效率、承载能力、温升、寿命等试验,并在航空等领域进行试验验证。考核指标:开发新型精密齿轮传动装置不少于3种 其中,零隙精密传动空载回差小于5角秒,传动误差小于60角秒 在相同试验条件下,承载能力、寿命等较现有传动提高20%。1.6高功率密度微纳振动能量收集器前沿技术研究内容:研究工业振动环境下,振动摩擦、振动压电、振动电磁的高效能量收集转换方法 研究微纳振动能量收集器的先进材料和高效能量收集结构设计技术 研究能量存储及低功耗调理电路设计与系统集成技术 研制高功率密度摩擦能量收集器、压电能量收集器、电磁能量收集器原型器件,并在工业现场无线传感网节点试验验证。考核指标:振动频率覆盖1Hz~500Hz,摩擦能量收集器峰值功率密度≥400μW/mm2,压电能量收集器归一化功率密度≥5μW/(mm3· g2),电磁能量收集器归一化功率密度≥0.5μW/(mm3· g2)。1.7跨尺度微纳米三坐标测量基础理论与技术研究内容:研究三维纳米位移和定位的测量理论与技术 研制高分辨力三维组合纳米测头 研究微纳三坐标测量机量值溯源技术 研究典型微型零件三维准确测量方法及技术 研制微纳米三坐标测量机样机,在精密微型零件加工和微纳制造领域进行试验验证。考核指标:微纳米三坐标测量机量程X× Y× Z≥100mm× 100mm× 50mm 三维测量分辨力优于1nm 最大允许误差(E3)(250+4.5× 10-6L)nm 实现宽度低至100μm的结构内尺寸及形状三维测量。2.共性关键技术类2.1工业机器人减速器轴承关键技术及工业验证平台研究内容:研究工业机器人减速器轴承的高精度及长寿命设计方法 研究薄壁及柔性等特殊轴承套圈批量化磨削、热处理等精密加工技术 研究工业机器人减速器轴承性能和寿命试验验证技术及装备 制定工业机器人减速器轴承试验技术规范 搭建工业机器人减速器轴承系列产品工业性验证平台,开展系列产品的寿命、摩擦力矩、振动、温升等试验,研究成果在工业机器人上实现应用。考核指标:开发工业机器人减速器轴承设计方法1套 RV减速器轴承精度达到P4级、试验寿命≥6000小时,谐波减速器轴承精度达到P4级,试验寿命≥8000小时 平台具备80mm~260mm内径轴承的寿命、摩擦力矩、振动、温升等测试能力,试验技术规范数≥1 在5家以上企业应用,装机系列数≥6。2.2大功率风电主轴及增速箱轴承关键技术及工业验证平台研究内容:研究大功率风电主轴及增速箱轴承的长寿命、可靠性设计分析技术 研究抗疲劳制造工艺等轴承控型控性技术 研究轴承性能和耐久性强化试验技术及装备 制定大功率风电主轴及增速箱轴承试验技术规范 建立大功率风电主轴及增速箱轴承系列产品工业性验证平台,开展寿命、振动、温升等性能试验,研究成果在大功率风电机组上实现应用。考核指标:开发风电主轴及增速箱轴承数字化设计软件≥1套 4MW以上风机主轴及增速箱轴承精度等级不低于P5,增速箱高速端轴承温度≤85℃,理论寿命、强化试验寿命≥20年 应用企业不少于2家,装机不少于10台套 平台具备200mm~1180mm内径轴承的寿命、振动、温升等性能测试能力,试验技术规范≥1套。2.3微小型液压元件关键技术研究内容:研究高功率密度电-机械转换器、低液动力阀口的设计和制造工艺 研究高功率密度液压泵旋转组件的设计和加工工艺 研究微小型液压阀和液压泵的性能测试方法 在航空航天、石油装备等领域进行试验验证。考核指标:研制不少于4种规格的高压微小型液压泵和液压阀样机,泵排量≤5mL/r,阀流量≤5L/min,响应时间0.5ms~1.5ms 制定微小型液压阀和液压泵性能测试规范2项 开发微小型液压阀和液压泵性能测试装备1套。2.4海工装备用长寿命耐腐蚀液压元件及系统关键技术研究内容:研究海洋环境下活塞杆耐腐蚀涂层技术与工艺 研究海洋环境下长寿命液压缸密封技术 研究液压控制系统的稳定性、工况适应性等关键技术,在大型海上风机、海洋平台升降与波浪补偿装置等海工装备中验证。考核指标:缸径250mm~650mm,活塞杆涂层弯曲疲劳试验≥500次(无裂纹),中性盐雾实验时间≥5000小时 研制2种以上典型海工装备用液压系统。2.5高性能机械密封关键技术与工业试验平台研究内容:研究机械密封关键元件表面精密成形、智能化监控与检测技术 研究高温高压多介质机械密封试验和综合性能评估技术 研究面向油、水和气介质的机械密封元件工业试验平台。考核指标:关键元件表面微槽深度误差不超过5%,曲面轮廓误差≤1μm,表面粗糙度Ra≤0.1μm 平台可进行高温高压多介质试验,具备线r/min的产品试验能力。2.6高速重载锥齿轮传动关键技术研究内容:研究高速重载弧齿锥齿轮传动的动态设计理论,系统动力学仿真与结构动力学优化 研究锥齿轮复杂齿面高效切齿和精密磨齿数字化仿真技术及软件 研究锥齿轮疲劳寿命加速试验技术 在航空传动领域开展应用验证。考核指标:开发不少于2类高速重载锥齿轮,转速≥8000rpm,单对齿率密度≥450kW/kg 齿轮加工精度高于5级,传动效率≥96%,寿命提高20% 开发高速重载锥齿轮数字化制造软件1套,高速重载锥齿轮疲劳寿命试验装备1套。2.7高长径比零件高效清洁热处理技术研究内容:研究高长径比零件热处理应力/变形演变规律、数值模拟与表面热处理强化机理及基础工艺,热处理表面强化层控制技术 研究高长径比零件高效感应热处理和真空热处理技术 开发高效清洁热处理装备,实现滚动部件等典型高长径比零件在微电子制造、航空航天等领域的应用验证。考核指标:高长径比零件感应热处理装备1套,可处理零件直径50mm~200mm、长度≥5m,可实现零件淬硬层厚度4mm~12mm、硬度均匀性≤± 1HRC、变形量≤1mm/m 线℃,有效加热区炉温均匀性≤± 5℃,压升率≤5× 10-1Pa/h,可实现零件硬度均匀性≤± 2HRC 感应和真空热处理及变形控制后的零件表面硬度均匀性≤± 1.5HRC,淬透层深度均匀性优于± 0.03mm。2.8清洁切削共性关键技术研究内容:研究高速干切工艺使能关键技术,建立基础数据库 研究微量润滑切削与低温冷却切削装置及相关功能部件 研究高稳定性清洁切削工艺技术及高生物降解微量润滑切削液 开展航空航天典型材料的清洁切削试验验证。考核指标:高速干切工艺基础数据库涵盖多种典型材料和工艺,及其相关的百种以上工况基础数据 适用于车、铣加工工艺的低温微量润滑装置及相关功能部件不少于6种,低温冷却切削装置的最低输出温度低于-190℃ 清洁切削机床周边悬浮颗粒物浓度≤.5mg/m3 切削液生物降解率≥95% 完成不少于3种典型材料清洁切削试验验证。2.9硅基MEMS高深宽比结构无损测量技术研究内容:研究MEMS高深宽比结构三维几何特征快速无损测量原理和方法 研究测量系统设计、光学显微传感、微弱信号采集与处理、校准与误差补偿、量值溯源等关键技术 研制高深宽比三维特征尺寸快速无损测量系统,并在MEMS工艺线试验验证。考核指标:沟槽深宽比≥20:1,深度测量范围10mm~300mm,深度测量不确定度≤0.5%(k=1) 线硅基MEMS厚金属薄膜关键技术研究内容:研究硅基MEMS厚金属薄膜工艺兼容性,研究高质量厚金属薄膜制造工艺、薄膜特性测试技术 研究硅基厚金属薄膜MEMS结构释放工艺技术,研究MEMS继电器的高可靠设计、制造及封装等关键技术 开发硅基MEMS厚金属薄膜成套制造工艺技术,在航空航天重大技术装备中应用。考核指标:硅基衬底圆片直径≥150mm,金属薄膜厚度≥5mm,薄膜厚度误差≤± 3%,薄膜应力≤150MPa MEMS继电器负载电流≥500mA,接触电阻≤500mΩ,开关寿命≥1× 106次,成品率≥85%。2.11高性能微纳温度传感器关键技术研究内容:研究耐高温柔性曲面衬底上薄膜材料热电特性、快速响应敏感单元设计技术,曲面衬底上高温温度传感器的高可靠性设计及制造关键技术 研究光学温度传感器回音壁谐振腔、模式调控、频率锁定等关键技术 研制曲面高温温度传感器和高分辨率温度传感器原型器件,并在航空航天重大技术装备中试验验证。考核指标:曲面衬底高温温度传感器测量范围-60° C~1800° C,误差≤± 1.5%FS,响应时间≤10ms 高分辨率温度传感器测量范围20° C~40° C,分辨力≤1μK/。2.12硅基MEMS气体传感器关键技术研究内容:研究硅基MEMS气体传感器芯片集成化设计技术 研究硅基MEMS红外光源、光学微腔、光学天线、红外探测器、温度传感器等核心部件与集成制造技术 研究标校算法、边缘计算、ASIC芯片闭环控制、环境效应等非色散红外(NDIR)气体检测系统集成关键技术 实现传感器在流程工业中应用。考核指标:气体传感器量程二氧化碳(0~5000ppm)、二氧化硫(0~100ppm)、氮氧化物(0~50ppm)、甲醛(0~100ppm)、丙酮(0~100ppm),测量误差≤± 2%。系统芯片尺寸≤20mm× 10mm× 5mm,长期稳定性≤1%FS/年,制定传感器规范或标准≥2项。2.13高性能磁传感器关键技术研究内容:研究并优化高性能磁传感器芯片制造工艺技术 研究高性能磁传感器的高灵敏结构设计和高可靠封装技术 研究磁编码器与转速测量涉及的ASIC芯片、软件算法、测控接口等 形成制程规范,在数控机床、工业机器人、伺服电机等装备应用。考核指标:磁传感器灵敏度100mV/V/Oe,本底噪声≤10pT/@1Hz,体积≤30mm× 30mm× 5mm,成品率≥85% 伺服电机磁绝对位置编码器精度优于0.02° ,成套制程规范≥2项。2.14仪表专用微控制器芯片设计及应用关键技术研究内容:研究数据采集、处理、存储、通信等高度集成的工业自动化仪表芯片设计技术 研究针对高度集成仪表芯片的软件可重用开发方法,开发典型功能库 研究仪表高密度集成设计等关键技术 基于上述芯片,开发核心零部件自主可控的温度、压力、流量、电动执行器等小型化仪表,并开展应用验证。考核指标:微控制器芯片模/数转换精度不低于16位,内嵌32位微处理器,内嵌HART、FF、Profibus等通信控制器 完成不少于100台小型化仪表应用验证。2.15多参数危险气体在线分析关键技术研究内容:研究在线分析仪器紧凑型核心部件高密度集成技术 研究含固、液杂质的工业气体在线测量预处理技术及装置 研究一氧化碳、二氧化碳、氧气、甲烷、硫化氢、氨气等多组分气体浓度、多参量集成测量技术 研制高安全多参数小型化危险气体在线分析仪器 在典型工业过程领域开展应用示范。考核指标:工业主要危险气体测量线%FS 温度在线℃,压力在线MPa 在冶金、石化、化工等两类以上工业领域的爆炸性气体环境危险区域开展应用示范。2.16六自由度激光自动精准跟踪测量关键技术研究内容:研究六自由度激光跟踪测量原理与方法,建立相应的数学模型,攻克目标捕获与跟踪、高精度绝对测距、高精度姿态测量、数据解算、性能校准与精度补偿等关键技术 研制六自由度激光跟踪测量原理样机,在机器人校准、飞机和燃气轮机装配等领域开展试验验证。考核指标:最大跟踪测量半径30m,空间坐标测量精度≤10ppm,姿态测量精度≤0.03° ,最大跟踪速度2m/s。2.17工业现场通信质量分析关键技术研究内容:研究典型工业通信协议的报文快速分析、在线通信质量评估与分析诊断技术 研究强干扰工业环境下工业通信物理层信号的多参数测量、环境干扰在线评估与分析诊断技术 研制工业现场通信质量分析仪器,在制造领域开展试验验证。考核指标:工业通信协议分析种类≥6种、工业以太网通信分析种类≥6种,通信质量分析报文覆盖率≥90% 仪器具备通信物理信号的电压差、抖动、上升时间、下降时间、比特时间、传输速率、传输延迟、同步精度等指标在线监测功能,具备数据链路层时间同步与MAC层、传输层、网络层和应用层分析功能,具备在线设备列表拓扑监视、错误报文率和循环通信调度分析等功能。2.18功能安全与信息安全融合的仪表共性关键技术研究内容:研究仪表功能安全和信息安全融合理论与方法 突破仪表冗余设计、失效诊断、故障控制、安全通信、访问控制、事件及时响应等关键技术 研制具有功能信息安全融合能力的变送器/执行器等仪表 在石油、化工、火电等典型行业开展应用验证。考核指标:仪表实现安全完整性等级SIL2,信息安全等级SL2,整体诊断覆盖率≥90%。3.应用示范类3.1工程机械大扭矩轮毂驱动关键技术及应用示范研究内容:构建大扭矩轮毂驱动系统多变工况下的载荷谱,研究驱动行星齿轮传动系统集成设计方法 研究轮毂驱动系统多体动力学及可靠性,轮毂驱动系统热平衡及传动效率 研究轮毂驱动系统零部件制造工艺与关键技术,在大型工程机械中应用示范。考核指标:载荷谱数据库1个,设计分析软件1套 大扭矩轮毂驱动系统扭矩≥1× 106N· m,减速比≥32,传动效率≥90%。3.2铝合金承力结构件挤压铸造成形技术及应用示范研究内容:开发适合车辆承力结构轻量化的铝合金高性能挤压铸造成形关键技术 建立铝合金挤压铸造成形材料—工艺—组织—性能仿真模型和测试平台 建立不同重量、形状、尺寸的挤压铸造产品开发试验平台 研究典型零件轻量化结构设计、工艺优化、性能评价技术,在车辆制造领域应用示范。考核指标:挤压铸造产品开发试验平台具备0.05kg~30kg或投影面积10cm2~3000cm2承力结构件的挤压铸造能力 铝合金承力结构件抗拉强度≥280MPa,屈服强度≥220MPa,延伸率≥8% 铸件尺寸精度≥CT6级 形成至少5种典型承力结构件的挤压铸造成形工艺示范生产线高强度铝合金大型薄壁件精密铸造技术及应用示范研究内容:研究铝合金精密铸件控形控性方法及精密铸件凝固控制技术、数字化精密铸造技术 研究铝合金高真空压铸技术 研制典型高强度铝合金大型薄壁件,在航空航天、汽车等领域应用示范。考核指标:铝合金铸件外形尺寸≥1.5m,300℃条件下抗拉强度≥185MPa、延伸率≥5% 大型铝合金框架类铸件关键尺寸精度CT7~8级,内部质量达I类要求。铝合金线kPa,铸件抗拉强度≥250MPa、延伸率≥10% 形成3种以上铝合金关键部件的生产应用示范。3.4高性能光栅位移传感器开发及应用示范研究内容:研究玻璃、石英、金属及陶瓷基底光栅的超长大幅面、可复制、高精度制造技术 开发超精密、大幅面、多自由度、宽温域的高性能系列光栅位移传感器 研究超高细分技术、信号处理与融合技术以及系统集成技术。完成光栅传感器的技术研发,并在精密制造和高端测量装备中应用。考核指标:线mm 角位移光栅分辨率0.01 ,精度0.2 ,光栅幅面最大外径500mm 二维光栅分辨率1nm,精度1μm,光栅幅面500mm× 500mm 宽温域位移传感器温度范围-60° C~1000° C,测量精度0.2mm,光栅长度20mm 产品成品率≥90%。3.5工业仪表制造过程智能标定系统开发及应用示范研究内容:研究压力和流量等仪表标定环境智能控制技术及装置 研究多批量、多品种仪表自适应装夹,仪表标定系统参数自配置,仪表参数自修正等关键技术 研制核心零部件自主可控的压力和流量等仪表制造过程批量化智能标定系统。考核指标:压力仪表批量标定最大允许误差0.015%,温度补偿范围覆盖-40℃~80℃,单次温度补偿台数≥50 流量仪表标定系统最大允许误差0.2%,单次标定台数≥10 在2家以上仪表制造企业开展应用示范。3.6芯片封装缺陷在线视觉检测仪开发及应用示范研究内容:研究自适应多模式照明、光学自动对焦、高速图像采集与处理、精准定位与同步控制、图像配准与三维重构、复杂缺陷识别分类等关键技术,研制高灵敏度半导体芯片封装缺陷在线视觉检测仪,开展应用示范。考核指标:仪器检测灵敏度优于0.5μm,最大检测运动速度100mm/s,缺陷检测准确率≥99% 在2家以上芯片生产企业开展不少于5套样机的应用示范。
前文回顾:近二十年我国齿轮量仪的发展(上)5CNC大齿轮测量中心和超大齿轮测量系统是CNC齿轮测量中心在大齿轮及超大齿轮测量的扩展和创新(1)1989年,工具所推出的局部CNC式1.2m大齿轮测量仪CZE1200D,如前所述,该仪器由单片式计算机控制步进电机二联动,首次实现齿轮量仪螺旋线的CNC数控数字化测量。其改进型为2015年的CZE1200DA齿轮测量仪(图24);图24工具所CZE1200DA齿轮测量仪(2)2004年,哈量国内首次开发2mCNC大齿轮测量仪CNC3929,改进型为CNCL200(图25);图25哈量L200CNC大齿轮测量中心(3)2011年,精达创新设计开发2.5mCNC大齿轮齿轮中心,其改进型为JLR300(图26),在国内创新采用了三坐标三联动(θ,X,Y)的渐开线成形原理,实现沿端面啮合线对大齿轮渐开线齿廓精度的测量,即“NDG”法向展成测量原理;精达公司将该原理创新应用于小模数齿轮的测量中,取得了良好效果。图26精达JLR300大齿轮测量中心(4)2017年,哈尔滨同和光学公司展出精密CNC大齿轮测量中心T150A(图27)。作为哈尔滨工业大学精密超精密加工和测量设备领域的科技成果产业化基地的哈尔滨同和光学展出的大齿轮测量中心,集成了超高精度气浮轴系、气浮托盘调心技术及直线电机驱动等先进技术。近年不少国产大型CNC齿轮测量中心,如哈量CNCL200(见图25)、精达JW型(图28)和智达ZD(图29)型大齿轮测量中心,都采用了5轴坐标系统结构布局,即径向坐标采用了上下二层,既简化机械结构又可减少测头阿贝误差,具有提高仪器稳定性和精度等优点。智达2020年新开发的Z系列大齿轮测量中心甚至采用了三种齿廓测量原理:法线极坐标、极坐标和啮合线测量原理,以适应不同用户需求。仪器采用全新分层控制理念的3U架构全闭环控制器实现动态位置全闭环控制,仪器性能得到了提升。图27哈尔滨同和T150A齿轮测量中心图28精达JW型齿轮测量中心图29智达ZD型齿轮测量中心(5)2013年,北京工业大学成功开发了用于超大齿轮的双测量装置集成综合测量系统——“激光跟踪+三维平台”在位测量系统(图30),首次进行了大胆创新和探索,在超大齿轮的测量理论、技术和实践上,取得了令人可喜的成果。(a)(b)(c)图30北工大超大齿轮旁置式双测量装置集成综合测量系统6自动化智能化齿轮测量分选仪器/系统实现CNC齿轮测量中心在齿轮生产现场在线年,工具所推出车间用齿轮在线三维双啮测量分选机CQPF2000,随后哈量—北工大也成功开发出3501齿轮分选机(图31),能在线实现批产齿轮径向综合三维误差测量及分选功能。图31工具所及北工大—哈量齿轮三维双啮测量机(2)2013年,精达为东风汽车变速箱生产线型齿轮自动分选机,用机械手实现半自动盘/轴类齿轮的双啮检测和分选。2015年精达、智达及金量展出风格迥异的双啮式齿轮自动/半自动分选机(图32)。2015年,南京二机床展出了由六轴机器人操作的“智能化齿轮加工岛”(见图5),在实现齿轮无人化双啮自动检测的同时,通过网络连结,能根据测量结果进行反馈,对系统中的数控滚齿机和剃齿机的加工参数进行智能化调整后再加工,实现批产齿轮闭环质量控制与制造,在我国圆柱齿轮制造业的数字化、智能化和自动化中树立了发展标杆。哈量于2017年推出具有时代感的3503齿轮分选机(图33)。此外还有2005年秦川机床推出的在数控磨齿机上的数字化在机测量装置,近年在国内也得到重视,国产全自动流水线齿轮分选机的开发发展迅速。其中,哈尔滨精达和智达(图34)都有相应产品系列相继问世,服务于齿轮制造企业。以上齿轮分选机基本上都是以齿轮双啮仪为检测仪器。在提升齿轮双啮仪的自动误差补偿功能上,精达于2017年展出了获得专利的补偿式齿轮智能双面啮合检查仪产品,既提高仪器测量精度也满足了国际市场标准要求,该双啮仪的补偿功能引起行业的关注与好评。(a)(b)图32精达半自动在线齿轮分选机(a)和秦川机床在机测量(b)(a)(b)图34精达JFE全自动流水线齿轮分选机(a)及智达2020年为浙江双环传动改造的日本制造桁架式齿轮在线年,智达为株洲齿轮有限公司提供了2台六轴机器人齿轮在线快速智能检测系统(见图6),集成了包括国产CNC齿轮测量中心和齿轮双啮测量仪以及意大利光学图像测量仪在内的3台检测功能各异的齿轮精密测量仪器,实现在线轴类齿轮零件的精度检测和质量统计及分选,充分显现了我国齿轮在线检测成套技术和装备的开发制造能力,在数字化、智能化和自动化方面已经提升到了一个崭新高度。7齿轮整体误差测量仪技术传承难能可贵,新的发展令人期待和鼓舞1970年前后,由工具所黄潼年为首的我国齿轮制造与测量业界众多科研技术人员共同努力,创新开发的成套齿轮整体误差测量技术,致力于研究分析,力图探索齿轮的几何形状及位置精度和齿轮的啮合运动综合精度之间的因果关联。齿轮整体误差技术目前可大致分为三类:即采用坐标式几何解析测量法的齿轮静态整体误差测量技术、采用啮合滚动点扫描测量法的运动态齿轮整体误差测量技术以及与虚拟数字化测量齿轮或虚拟数字化配对工件齿轮进行啮合滚动的虚拟啮合滚动点扫描测量技术,三者都归类于运动几何测量原理。测量项目有:静态齿轮整体误差曲线族、运动态齿轮整体误差曲线族以及虚拟齿轮整体误差曲线族。期待今后会有传动动力态齿轮整体误差测量技术及相应曲线年,工具所持续开发锥齿轮整体误差测量技术,建立了锥齿轮局部互换性测量的相对测量体系,实现锥齿轮齿廓二次局部基准误差的补偿(图35),曾应用于青岛精锻齿轮厂。(a)(b)图35工具所锥齿轮整体误差测量仪及局部互换性测量体系(2)至2007年,工具所不断改进并生产齿轮整体误差测量仪系列产。